How L6 Elite Works?
L6 Uses The Five Step DMAIC Process That Includes: Define, Measure, Analyze, Improve, and Control.
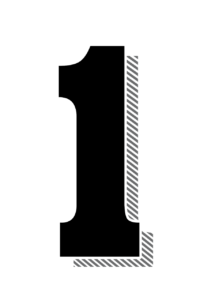
Define
- Objective. Clearly define the problem or opportunity for improvement. Identify the goals and scope of the project.
- Outputs: Develop a project charter that outlines the project's purpose, scope, resources, timeline, and expected outcomes. Define customer requirements and expectations.
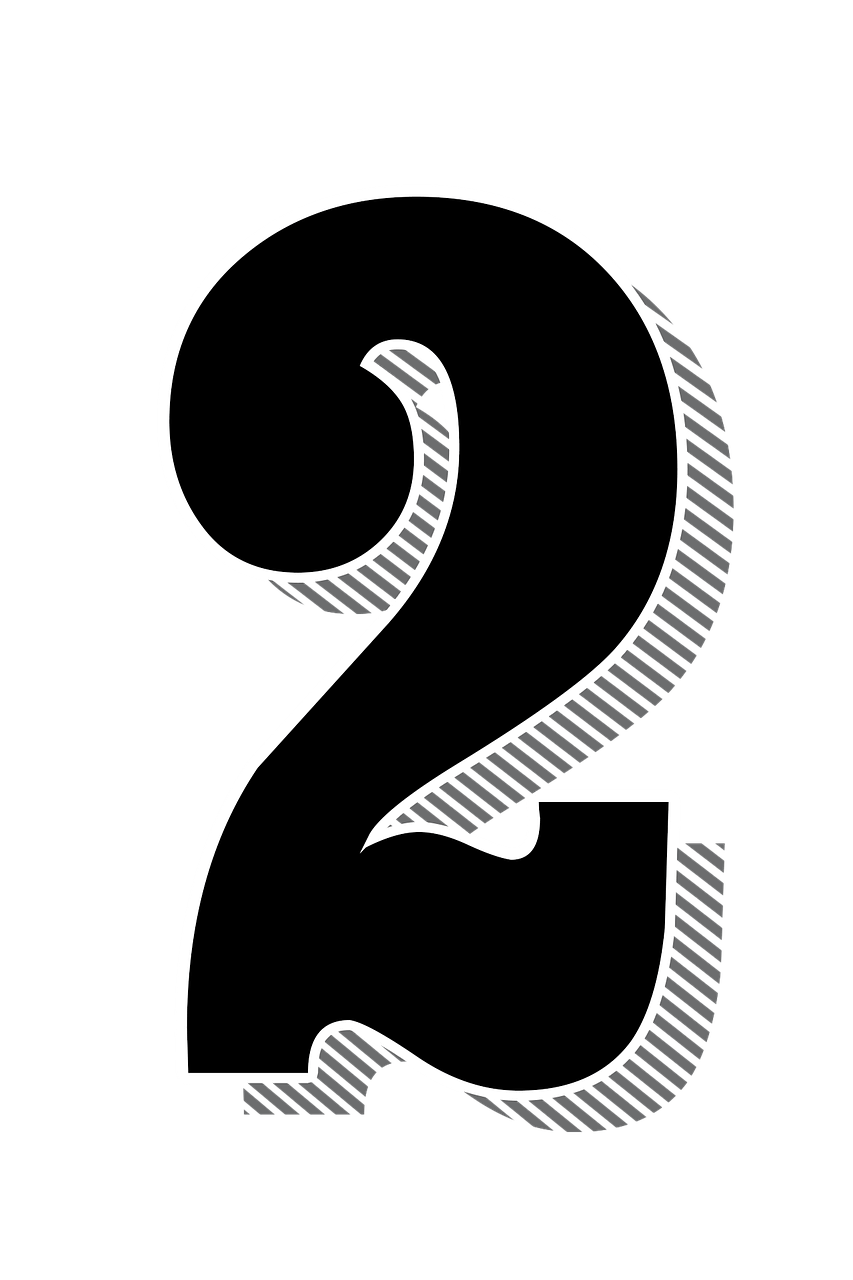
Measure
- Objective: Measure the current performance of the process to establish a baseline and quantify the extent of the problem.
- Outputs: Identify key process metrics (KPIs) and collect relevant data. Validate measurement systems and ensure data accuracy. Create detailed process maps to understand the flow and interactions within the process.
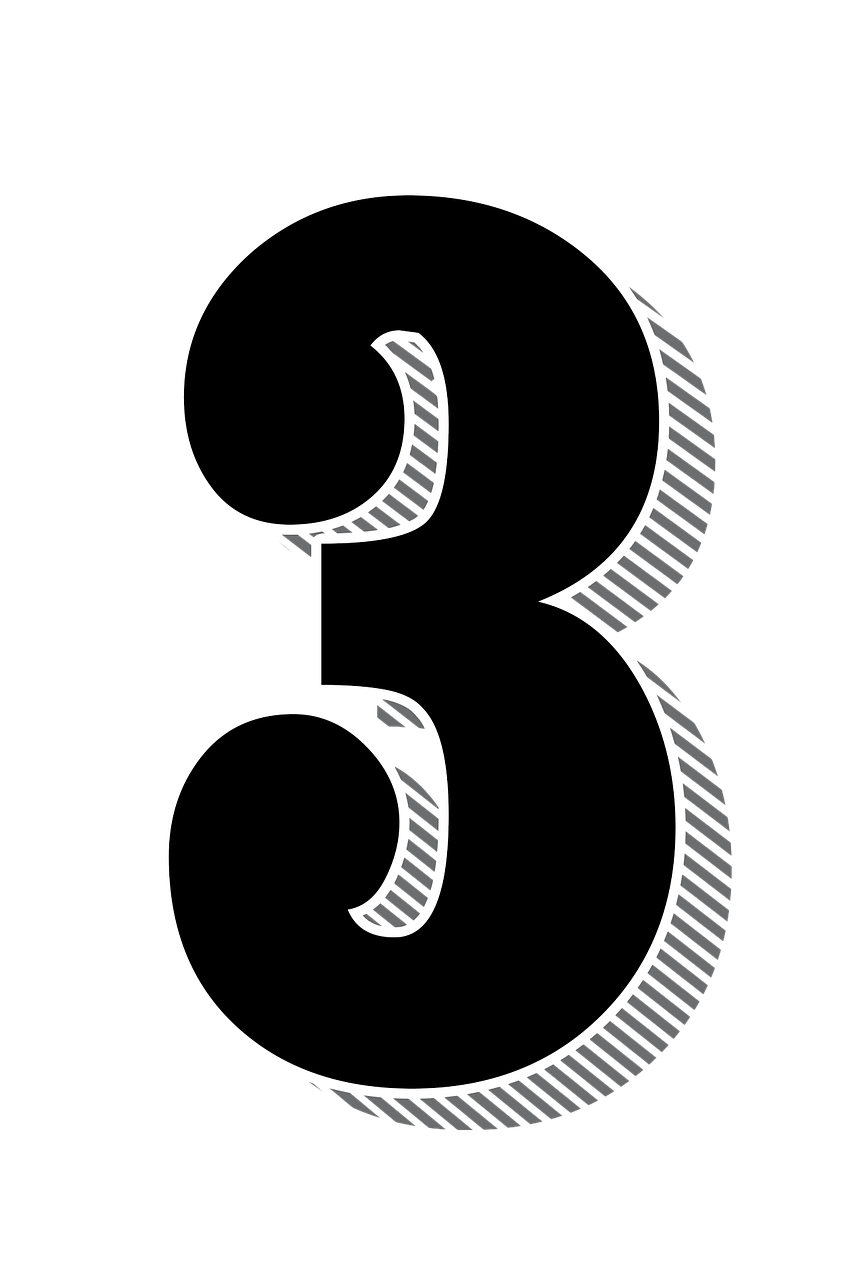
Analyze
- Objective: Analyze the data collected to identify the root causes of defects or inefficiencies in the process.
- Outputs: Use statistical tools and techniques (such as Pareto charts, histograms, KPI Analysis, and hypothesis testing) to analyze data and identify potential causes of variation or problems. Prioritize root causes based on their impact on the process.
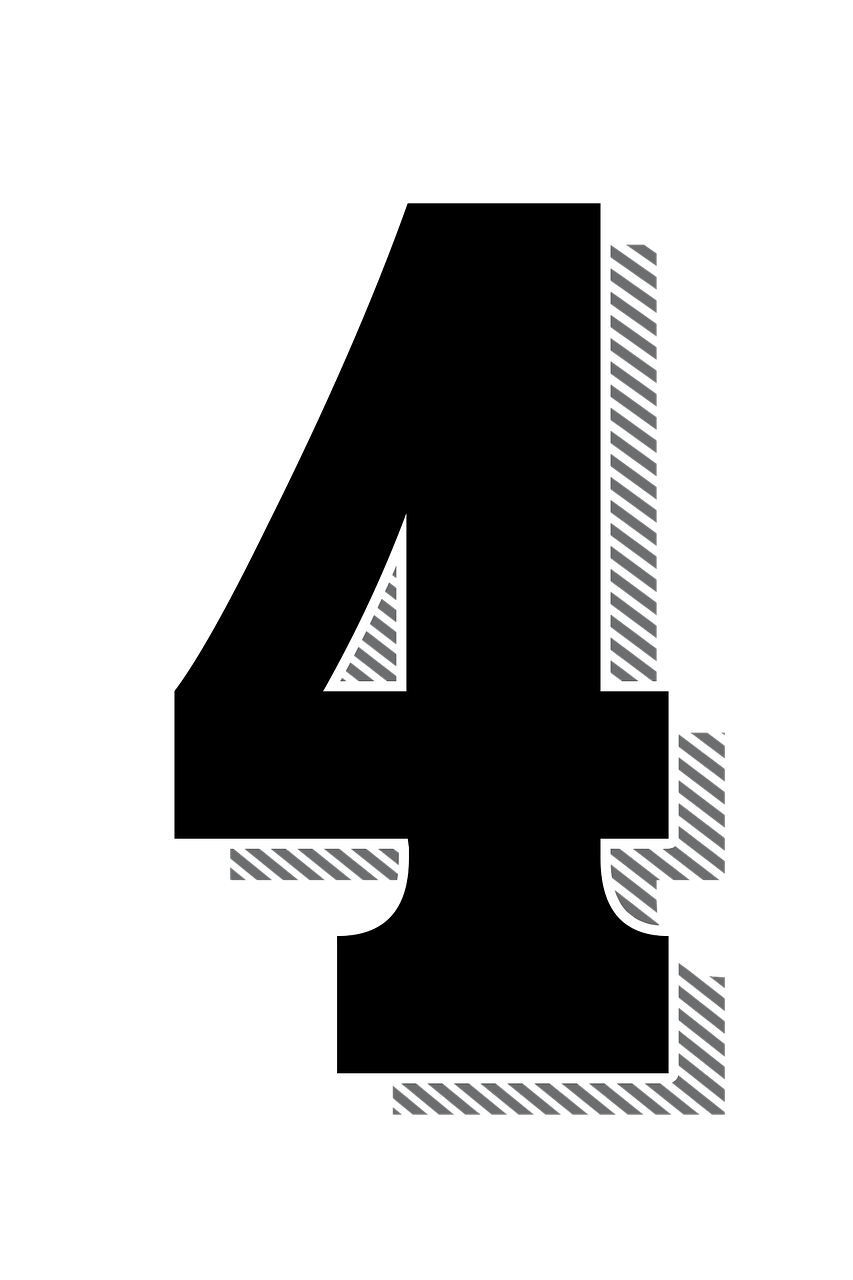
Improve
- Objective: Develop and implement solutions that address the root causes identified in the Analyze phase to improve the process performance.
- Outputs: Generate, evaluate, and select potential solutions. Design and pilot test process improvements. Implement the selected improvements and verify their effectiveness using KPI analysis.
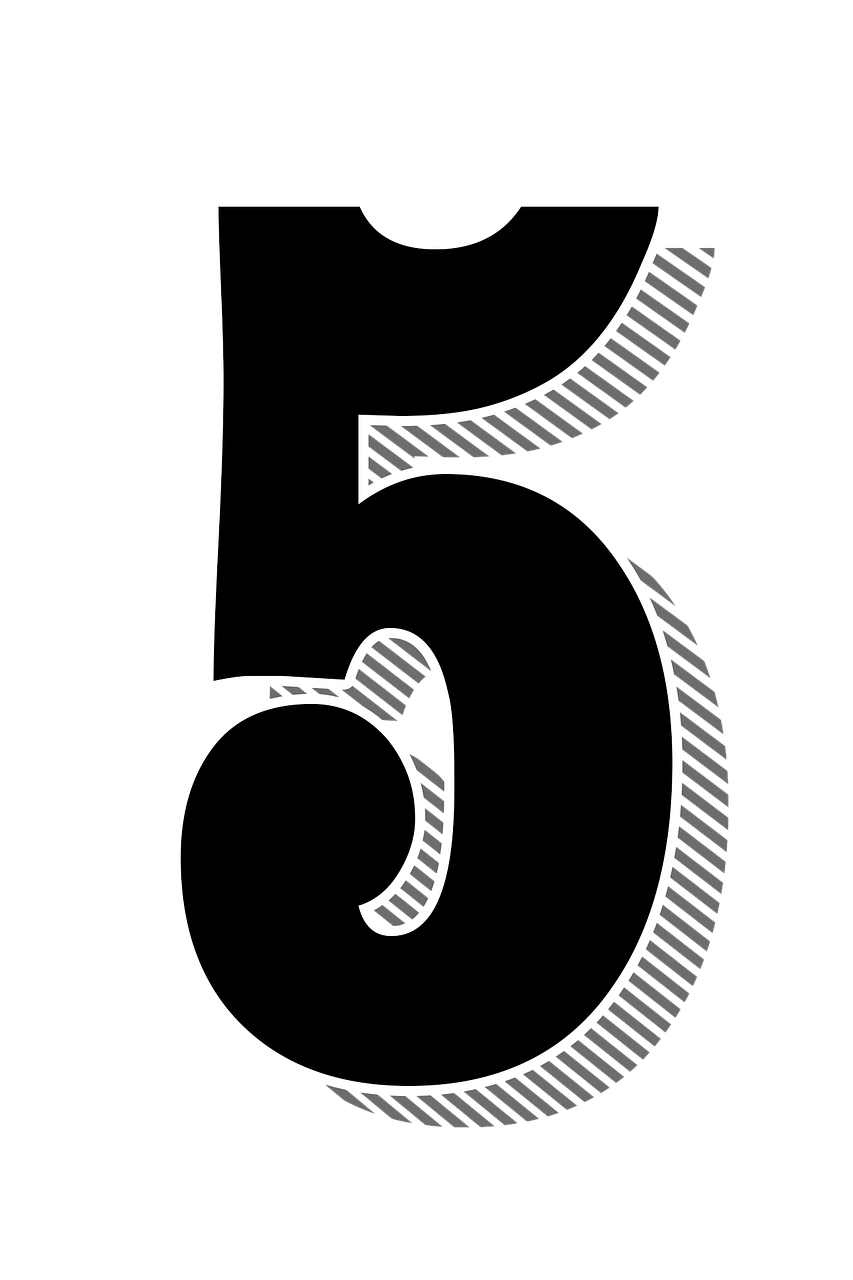
Control
- Objective: Establish controls to sustain the improved process performance over time.
- Outputs: Develop a control plan to monitor key process metrics and ensure that the process remains stable and within specifications. Implement standard operating procedures. Provide training and SOP to sustain the improvements. Plan for ongoing measurement and continuous improvement.
Key Industries
Lean Six Sigma methodology is widely applicable across various industries where quality control and process improvement are critical. Some of the industries that commonly use Lean Six Sigma include:
Telecommunications:
Companies in this sector use Lean Six Sigma to optimize network performance, improve call center efficiency, and reduce service downtime.
Information Technology:
IT companies employ Lean Six Sigma to enhance software development processes, improve system reliability, and streamline project management.
Retail:
Retailers use Lean Six Sigma to improve inventory management, optimize supply chain processes, and enhance customer service.
Pharmaceuticals:
Pharmaceutical companies apply Lean Six Sigma to ensure consistent product quality, improve manufacturing processes, and meet regulatory requirements.
Education:
Educational institutions use Lean Six Sigma to streamline administrative processes, improve student services, and enhance educational outcomes.
Manufacturing:
This was where Lean Six Sigma originated, particularly in sectors like automotive, electronics, aerospace, and heavy machinery.
Healthcare:
Hospitals, clinics, and healthcare providers use Lean Six Sigma to improve patient care, reduce medical errors, and streamline processes.
Finance:
Banks, insurance companies, and financial institutions use Lean Six Sigma to enhance operational efficiency, reduce errors in financial transactions, and improve customer satisfaction.
Government:
Government agencies use Lean Six Sigma to improve service delivery, reduce bureaucratic inefficiencies, and enhance public sector operations.
Energy:
Companies in the energy sector apply Lean Six Sigma to optimize energy production processes, improve safety protocols, and reduce environmental impact.